Aerobotix has created a sophisticated multi-axis robotic device with a lengthy carbon fiber arm that can access the F-22 Raptor engine inlet ducts in great detail
When performing depot maintenance at the Ogden Air Logistics Complex at Hill Air Force Base (AFB), Utah, the U.S. Air Force (USAF) Small Business Innovation Research program developed robotic technology that will soon make the process of restoring specialized coatings on F-22 Raptor engine inlets more efficient for aircraft maintenance personnel.
The project has been a collaborative effort between engineers from Wright-Patterson AFB and Hill AF as well as the Air Force Life Cycle Management Center’s (AFLCMC) F-22 System Program Office. According to Bryan Ripple of the 88th Air Base Wing Public Affairs article Robot technology developed for F-22s.
According to Colin Allen, an AFLCMC F-22 structure and system safety engineer at Hill AFB, this project has three main goals: reducing the number of hours aircraft maintainers are required to work in confined spaces while wearing full personal protective equipment, improving consistency and overall quality of the coatings applied and reducing the overall hours required to restore the inlets for the lifecycle of the aircraft.
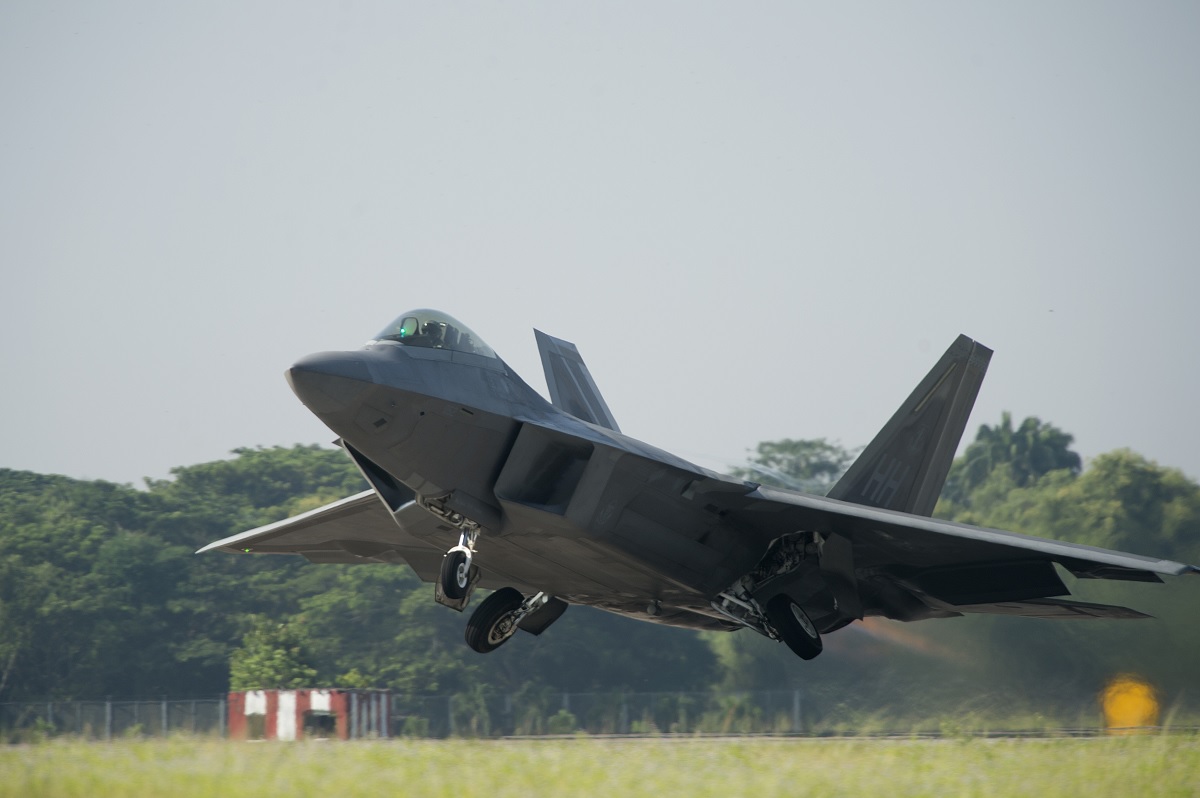
Aerobotix created a sophisticated multi-axis robot system with a long carbon fiber arm that can reach far into the engine intake ducts to handle these jobs. Currently, to manually recoat the intakes, maintainers must crawl inside them while wearing a Tyvek suit and respirator.
“It’s not an easy process. It’s kind of an awkward position to be in for a lengthy amount of time where the environment is actually considered a confined space here at Hill, so you need another person watching the person manually restoring the intakes,” Allen said.
“The actual removal of coatings from the F-22 inlets remains a manual process where maintainers go inside the intakes and strip the coatings using hand tools,” said Tech. Sgt. Justin Daywalt, the low observable/structures integrated support manager for the F-22 System Program Office at Hill AFB.
According to Carl Lombard, a materials research engineer with the Electronics & Sensors Branch, Manufacturing & Industrial Technologies Division, Materials & Manufacturing Directorate at AFRL, this creative project has made use of computing power through modeling and simulation to achieve the goals for the depot F-22 maintenance team.
“This enables the maintainers to avoid collision with the inlets and the plane while developing the fastest paths to correctly apply the coatings,” he explained.

“We’re producing fifth-generation aircraft maintenance capabilities for fifth-generation fighters,” said Allen.
Noteworthy that Aerobotix employees have used their knowledge of the procedure to make the switch to robotic intake coating repair for the F-22 as easy as feasible for everyone concerned.
“One of the reasons Aerobotix was chosen is because they’re certainly an industry leader as far as aircraft robotics goes in their use of robotics for aircraft maintenance on the F-22 and F-35 (Lightning II) programs. They have certainly been more than accommodating, to not only the AFRL and the SPO’s needs, but also the depot’s needs, as far as maintaining their schedule and reevaluating when they need to be in the depot doing work and during the validation process,” said Allen.

Photo by Tech. Sgt. Ryan Crane, Tech. Sgt. Jason Robertson and Tech. Sgt. Dana Rosso / U.S. Air Force